Why don’t you make the heavy-duty cement blocks you need with your own hands? This is a very simple undertaking provided that there is enough time and sufficient space to sink a certain number of them at the same time. Unlike most commercial heavy-duty cement bricks, yours will be full, and therefore a little heavier.
For the manufacture of cement bricks, it is worth noting the difference between a concrete block bearing (structural) intended to support loads in the construction of dwellings, and a freestanding block for partitions and interior divisions.
Above all, it is important to note that the production of hollow or solid cement bars of high quality is not difficult, provided you have enough skills even without the machine.
Although block-making machines are available even for DIY enthusiasts, they are not really needed unless you have a plan to run a masonry business. But if you only need the blocks for your home projects, there is no need for a machine.
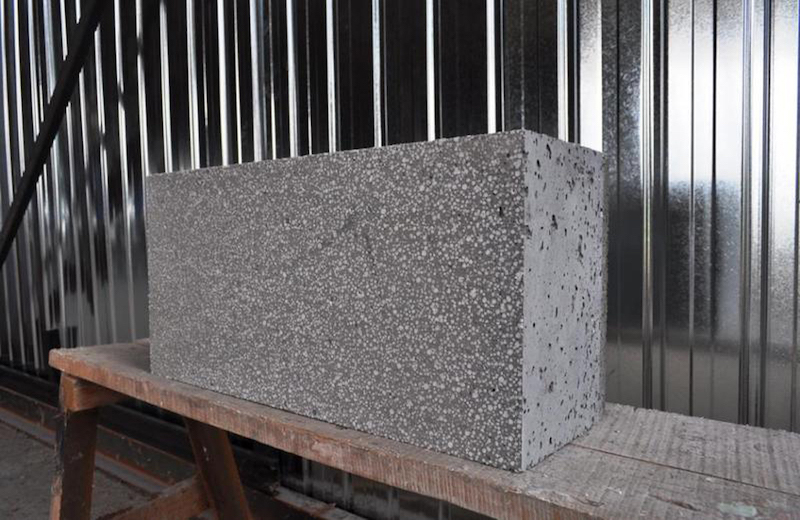
Why make your own concrete blocks?
There are many reasons why you should build your own cement bricks, as opposed to buying a manufactured product with standard sizes. By creating your own, you can perfectly size the block based on what you need. Here are some of the advantages why you should make your own heavy-duty cement bricks.
- Measurement and sizes
Ready-made concrete products sold in construction supply stores have standard sizes. They are good if you are repairing or replacing a portion of your wall. But if you are building a new project, for example, a chicken coop, or a fishpond where the space has uneven measurement or limited, you will run into trouble if you use standard-sized blocks. But by making your own, you can pre-design something that would fit the area where you want to build your project. You can build blocks with uneven sizes, especially for corner curves. You can’t find these types of blocks in hardware and construction supply stores.
- Cost-effective
Yeah, you hear it right. Building your own blocks will cost lower than buying pre-made ones. The reason why pre-made materials cost more is because of the labor and other overhead costs. Of course, you will spend some time making your own but by doing so, you are paying yourself instead of paying other people.
- Better quality
By building your own, you can push the quality to its limits. You can make a harder and stronger product. Most of the pre-made casts are made of a 1×3 mixture (1 cement and 3 sand). If you built it by yourself, you can make it stronger by mixing 2 part concrete cement and 1 part sand, or 2 part sand and 1 part concrete cement. Either way, your product will be more durable than those sold in the market.
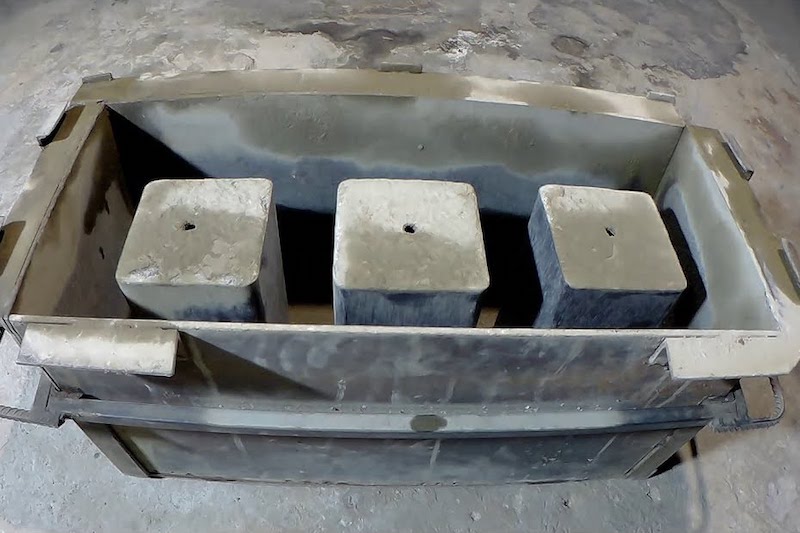
How to make a heavy-duty concrete block without a machine
The first thing you need is the necessary tools and materials. Spade, mason’s trowel, and square trowel are the basic and most important tools. You will also need a claw hammer and hand saw or circular saw for mold making. You may also need mason’s clamps for building the mold.
Materials
- Plywood – you need plywood for mold creation. Of course, you cannot make bricks without a mold.
- Nails – need to fasten the plywood to make molds
- Sand and gravel – the main material needed to make cement bricks.
- Concrete cement – concrete cement is the main sticking ingredient in order for the sand and gravel to stick together to form a block.
- Water
Preparation
Avoid dirt floors, and prefer concrete floors. To prevent the mixture from sticking to the ground, as for the pouring of garden slabs, one or more sheets of newsprint between the mold and the soil. A polyene leaf will also be suitable.
The mold for concrete blocks
This mold will actually be very close to a simple formwork. It will consist of four planks 27 mm thick, 50 x 20 cm, and 20 x 15 cm. Their assembly will be done with the help of mason’s clamps (to the rigor, large-open carpenter’s clamps will also do the trick). Cups nailed to the corners on the outside of the mold will strengthen it. For a large number of blocks, you will make a mold allowing you a series casting, consisting of two planks of high thickness, 2.50 m long, between which you will place six planks 15 cm long that will constitute as many separations. They will be held in place by nails, the large planks being wedged with the bricks.
If you want to use the blocks on a specific project that requires different measurements, you can also build a mold with customized measurements. The mold-making is the key based on your target application.
Mixing the concrete
The amount of sand, gravel, and concrete cement you are going to mix will depend on the number of molds you have. If you have 5 molds and want to pour the mixture on all of them at the same time, you need to estimate how much mixture each hole will need to film a concrete brick.
To mix, put 2 parts of fine sand and 1 part of fine gravel and then add 1 part concrete cement. Mix them with the spade and dose with water while the mixing continues. Once wet and properly mixed, pour the mixture into the molds.
Waste and pouring concrete
You will have to spoil it with enough water so as to get concrete of fairly hard consistency that you will sink into the mold in successive layers that you will take care to groom. Given this consistency, the hardened mixture can be unmolded within minutes. However, you will not handle it until twenty-four hours later. During drying, protect the mixture from the effects of wind and sun. Wet them regularly with a rain-set spray to prevent the draining water from evaporating too quickly, which would weaken them.